Reverse engineering is a powerful technique that allows engineers to analyze and recreate outdated components, effectively breathing new life into legacy systems. In this article, we’ll explore the importance of reverse engineering in the world of legacy systems and obsolescence management, and how skilled engineers ensure the continued operation of vital systems in various industries, including aerospace and defense.
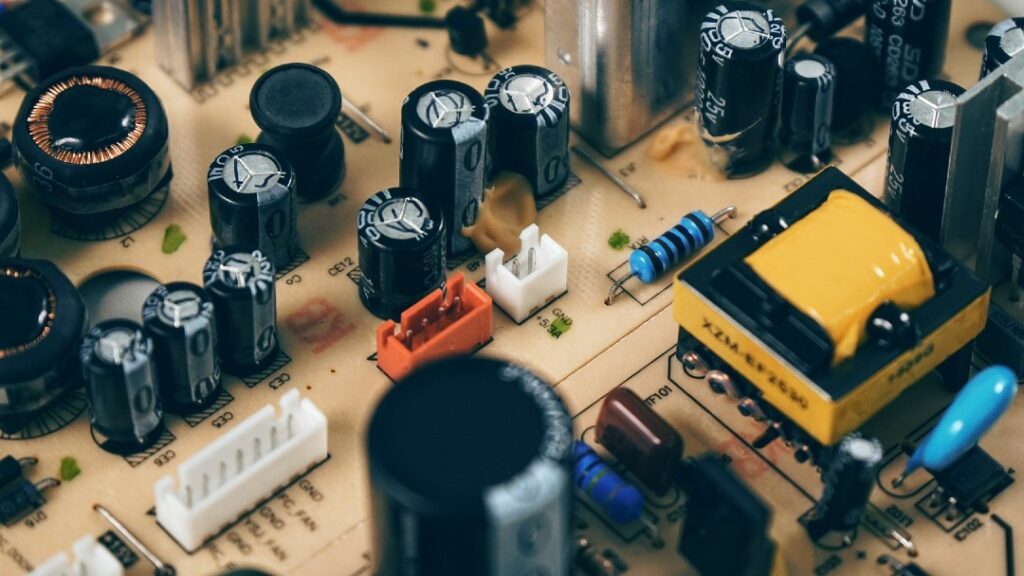
The Importance of Reverse Engineering
As technology continues to advance at an unprecedented pace, many industries rely on legacy systems and equipment that have been discontinued or are no longer supported by manufacturers. These systems often play a crucial role in operations, and replacing them with newer technology may not always be feasible or cost-effective. Reverse engineering becomes essential to keep these systems operational, especially when replacement parts or documentation are scarce or non-existent.
The Process of Reverse Engineering
Reverse engineering involves the systematic deconstruction of a device, component, or system to understand its design, function, and operation. Engineers start by examining the physical structure and components of the system, often using sophisticated imaging techniques, such as X-rays or CT scans, to visualize the internal workings without damaging the device. The next step is to create a detailed schematic or blueprint of the system, which can then be used as a reference for reproducing the components or designing replacements.
Once the original design has been thoroughly analyzed, engineers can begin the process of recreating the components. This may involve fabricating custom parts using advanced manufacturing techniques, such as 3D printing or CNC machining, or modifying existing components to fit the specific requirements of the legacy system. Throughout this process, engineers must ensure that the newly created components meet the same performance and quality standards as the original parts.
Challenges and Solutions
Reverse engineering can be a complex and time-consuming process, particularly when dealing with older, undocumented systems or proprietary technologies. Engineers must overcome various challenges, such as deciphering outdated or obsolete components, recreating parts with limited information, and ensuring compatibility with the existing system.
To address these challenges, engineers often leverage a combination of cutting-edge technology and extensive industry experience. Advanced tools, such as 3D scanning and modeling software, can help engineers capture detailed information about a component’s structure and dimensions, while collaboration with other experts in the field can provide valuable insights and knowledge on specific systems or components.
Conclusion
Reverse engineering plays a crucial role in the maintenance and longevity of legacy systems across various industries. By employing skilled engineers and advanced technology, businesses can effectively manage obsolescence and extend the life of their critical systems. In a world where technology is rapidly evolving, the art of reverse engineering allows us to bridge the gap between the old and the new, ensuring that vital systems remain operational for years to come.